The Transformation of Manufacturing: Production Efficiency Leads to Growth
- Peak Performance
- Jan 25, 2022
- 8 min read
This article is based on the findings in the report, Understanding the Impacts of Industry 4.0 on Manufacturing Organizations and Workers, prepared for the Smart Factory Institute and written by Chris Cunningham, PhD, UC Foundation Professor of Psychology, and Scott Meyers, Graduate Assistant, Psychology Department & Smart Factory Institute, from the Industrial and Organizational Psychology Department at the University of Tennessee at Chattanooga.
Over the past few decades, organizations have also been focusing on creating more efficient and production-related supply chains. Many manufacturing organizations are looking at “near-sourcing” and increasing their local production (Brutto, 2012; ISM, 2021). This has especially been a focus as the COVID-19 pandemic has created issues in various parts of the supply chain such as docking (ISM, 2021). These challenges are also likely to grow in complexity as the push for “mass-customization” and quick turn-around times for products to consumers becomes increasingly emphasized in Industry 4.0 (Statista, 2021). Additionally, larger quantities of components are being made at parts facilities and delivered to assembly plants on a just-in-time basis consisting of daily and even hourly orders (Industry Survey; CFRM).
Manufacturers in all sectors are also focusing on lowering production costs, especially in automobile production (Nelson et al., 2021). One way they are doing this is by using fewer parts through better quality control and error reduction in production processes (Nelson et al., 2021). A key strategy enabling this for many manufacturing organizations is the increased use of subassemblies (i.e., units assembled separately to be fitted with other completed units), which effectively reduces the number of parts involved in the ultimate production lines. Though commonly used in automobile manufacturing, this approach has utility in nearly all discrete manufacturing domains. In manufacturing domains that are more continuous in nature (e.g., food/beverage, chemical), similar efficiencies can be achieved with the use of batching methods. These types of workflow improvements help to reduce production times and increase overall quality of the end product.
Another trend within automobile and some other sectors of manufacturing is more regulation compliant and sustainable production processes (Hernandez-de-Menendez et al., 2020). Manufacturers are minimizing industrial waste and pollution (Nelson et al., 2021). Practices such as energy efficiency are saving costs and resources while also contributing to more sustainable manufacturing systems. Stricter regulatory environments regarding CO2 emissions are increasing in Europe and other areas that also contribute to this trend (Nelson et al., 2021).

CUSTOMER EXPERIENCE
The consumer-side of manufacturing is also changing. The technologies associated with Industry 4.0 affect the customer experience by not only shortening production times, but also by using internet-connected smart products and services to gather more complete and higher value data that helps manufacturers more fully understand customer needs, preferences, and usage patterns. This new level of interconnectedness allows for personalized selling and marketing strategies, as well as new ways of designing and producing products to meet actual instead of anticipated consumer needs. This heightened level of connectivity between manufacturing organizations and their consumers can also lead to more efficient product support (Statista, 2021). End users will begin to experience more personalized products, faster delivery, and lower prices (Statista, 2021), developments that are likely to be even further enhanced over time under Industry 5.0.
REVENUE MODELS
Operating under Industry 4.0 will also present manufacturing organizations with new opportunities to develop new revenue streams and improve overall machine and technology designs. Predictive maintenance (facilitated by the IoT and associated AI/ML based tools) will help equipment suppliers and end-user manufacturing organizations prevent faults before they occur. This will also create new revenue streams for the suppliers who are providing service on their machines and for manufacturers supporting products owned by end-user consumers. Examples of new revenue models include the monetization of data and a new emphasis on service-based revenue models, opposed to existing product-based models (Statista, 2021). The connectivity between manufacturers and consumers noted in the preceding subsection also creates new opportunities for more responsive product design and service provision that address specific needs as identified by data shared through the connected systems characteristic of Industry 4.0.
RELIABLE SUPPLY CHAINS
A highly influential area of development under Industry 4.0 is the evolution of the traditional supply chain and creation of a more connected, smart, and agile system for connecting suppliers to producers to customers (Statista, 2021). Supply chain and logistics technologies reduce the siloed processes within the various parts of the supply chain ecosystem such as product development, manufacturing, and distribution. As Industry 4.0 becomes more widely adopted, the supply chain will become more connected with real-time information flow, leading to improvements in just-in-time deliveries and reduced inventories. This creates a more integrated and transparent system. Examples of positive developments along these lines include autonomous logistics and warehousing (Statista, 2021).
SUSTAINABLE PROCESSES
Shet and Pereira (2021) argue that smart factories under Industry 4.0 will be more efficient and compliant with sustainability regulations and best practices. Sustainability has become an increasingly significant goal. For example, the United Nation’s 2030 Agenda for Sustainable Development calls for collective sustainability action (United Nations, n.d.) Industry 4.0 technology such as artificial intelligence is projected to have a positive environmental impact. Examples of this include reduced pollution and greenhouse gas emission (Lopes de Sousa Jabbour et al., 2018). Digital footprint data and traceability analysis can be used to identify and reduce environmental impacts of production. Increased energy efficiency is also associated with Industry 4.0 production as digital technology becomes more integrated, increasing equipment effectiveness and reducing energy waste (Shet & Pereira, 2021).
ADVANCED MANUFACTURING TECHNOLOGIES
In general, Industry 4.0 involves work being done in a digitally interconnected and technology-intensive environment where constant real-time data exchanges take place (Hernandez-de-Menendez et al., 2020). Essentially, all technological components of manufacturing production systems have the potential to be transformed or otherwise enhanced due to the digitalization that is at the heart of Industry 4.0 (Statista, 2021). Ultimately, the development and implementation of advanced manufacturing technology leads to improved decision-making, better monitoring of production, more efficient use of resources, and more accurate forecasting of demands (Hernandez-de-Menendez et al., 2020). Interconnected systems and vast data sets lead to faster and better-quality decisions and flexibility.
Industry 4.0 has introduced and integrated a variety of technology developments into manufacturing processes. In a fairly recent industry profile report, some of the highest levels of technology adoptions included ML (87%), big data analytics (84%), the IoT (82%), cloud computing (76%), web-based application utilization (76%), augmented and virtual reality tools (71%), wearable electronics (61%), and 3D printing (61%) (World Economic Forum [WEF], 2021). Additionally, in a Deloitte survey of 500 global senior manufacturing executives, advanced manufacturing techniques were ranked by future importance (Deloitte, 2021; Statista, 2021). In this ranking, predictive analytics, IoT with smart/connected products, advanced materials, digital design/simulation/integration, computing, advanced robotics, and additive manufacturing were all highly ranked by these subject matter experts in the U.S., China, and Europe (Deloitte, 2021; Statista, 2021). It is important to note, however, that although leaders of manufacturing organizations may be increasingly ready to adopt Industry 4.0 technologies, the same is not necessarily true within the broader workforce in which there continues to be concern and lack of understanding about the impacts of these technologies on the actual manufacturing workers.
LOWER PRODUCTION COSTS
Diverse smart devices can connect and respond to data from existing machine component sensors. A real-time data transfer connection can also be established among production machines. Sensors and wearables integrating the Internet of Things (IoT) have also increased connectivity to various products and components. Already these technologies are being incorporated into tools for monitoring and protecting worker safety and managing production efficiency. It is also conceivable that these technologies can support more precise monitoring and more effective management workers’ more general capabilities and health. All of these advancements can simultaneously support organizational efforts to improve operational efficiency.
The data gathered and used in these connected systems can support advanced artificial intelligence (AI) and machine learning (ML) technologies that can guide robotics and other forms of advanced automation to make the production processes of all forms more efficient by increasing precision, reducing human error, and fixing errors on a real-time basis using software. For example, real time data analysis will allow for continuous improvements in processes and machine design. Support and maintenance functions are also affected as remote and on-site support will help decrease machine downtime. Ultimately, more efficient manufacturing plants will lead to lower costs, less machine downtime, faster production, and higher production yield (Statista, 2021).
A 2021 Statista Market Outlook Report notes the interconnectedness of manufacturing system elements and greater production efficiency will ultimately result in increased energy efficiency and input optimization. Examples of this include waste reduction and a more circular economy production model that involves sharing and reusing products and materials. These types of changes will also lead to operational cost reductions through flexible/decentralized production, supply chain connectivity, and more agile organizations. Additionally, the industry will see improved capital utilization; example methods include predictive and automatic system maintenance leading to less machine downtime and lower inventory rates. Statista (2021) finally notes increased employment quality and linkage to services. This will be accomplished as work conditions/worker safety is improved via technologies such as robotics and as the workforce develops new skills and task efficiencies to provide more services to consumers (Statista, 2021).
The 2021 Statista Market Outlook Report also notes that Industry 4.0 involves a shift towards mass customization rather than simply an extension of the traditional focus on mass production. This reinforces the theme of production efficiency, which can support increased on-demand production and reductions in unused inventory (Statista, 2021). With these advancements in production efficiency, many manufacturers that have adopted Industry 4.0 practices are reducing their costs by focusing on optimizing and standardizing their capital and physical assets and aligning these resources to support this type of mass customization production model rather than simply increasing their mass quantity production (Statista, 2011). Examples of this include streamlining supply chains and increasing local production, but also developing a more skilled workforce that can fully utilize the advanced technologies noted above (Statista, 2021). Both of these examples involve optimized use of organizational assets in such a way that is aligned with this new production focus and Industry 4.0 theme of mass customization.
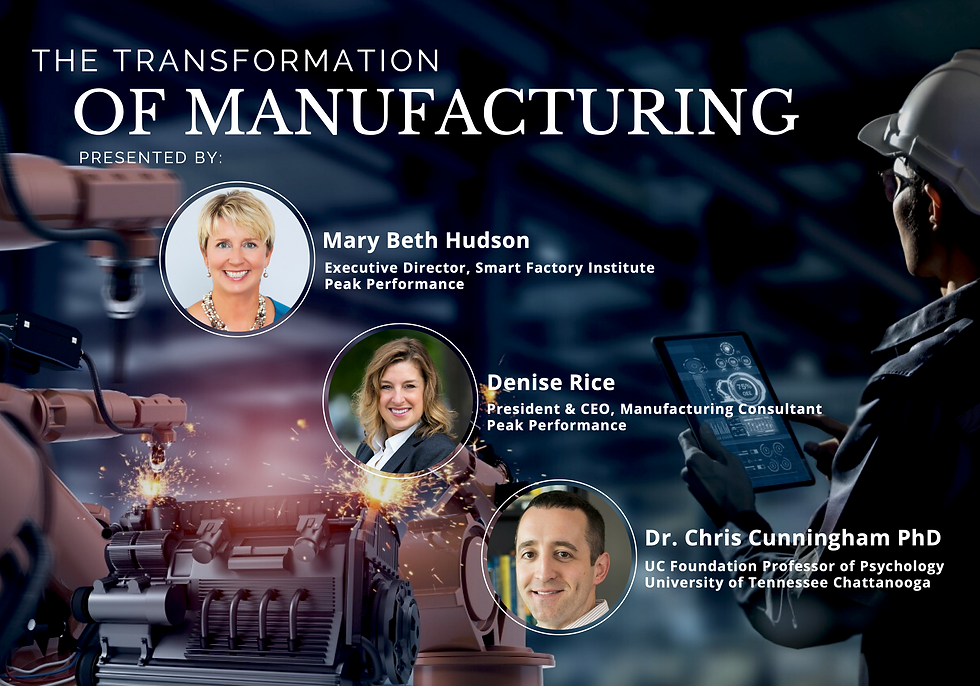
Join us LIVE as we explore the current manufacturing industry and the challenges and opportunities it faces in the midst of the adoption of Industry 4.0. The Transformation of Manufacturing will be a 3-stop tour across the state of Tennessee with stops in Jackson, Chattanooga, and Smyrna beginning February 2, 2022.
Each session builds on the prior session. In-person and virtual attendance options are available. Join us in person at your local session and virtually for the other two sessions!
February 2, 2022 | 7:30am - 8:30am (CT)/8:30 - 9:30am (ET)
Location: Jackson Chamber of Commerce, 197 Auditorium Street, Jackson, TN 38301 In-Person & Virtual Attendance Options Available
February 9, 2022 | 7:30am - 8:30am (CT)/8:30 - 9:30am (ET)
Location: LIVE from the Smart Factory Institute, Chattanooga, TN
Virtual Attendance Only
February 16, 2022 | 7:30am - 8:30am (CT)/8:30 - 9:30am (ET)
Location: TCAT Smyrna/Nissan Training Center, 663 Ken Pilkerton Dr., Smyrna, TN 37167 In-Person & Virtual Attendance Options Available
Sessions are free to attend, registration is required.
This tour is based on the findings in the report, Understanding the Impacts of Industry 4.0 on Manufacturing Organizations and Workers, prepared for the Smart Factory Institute and written by Chris Cunningham, PhD and Scott Meyers from the Industrial and Organizational Psychology Department at the University of Tennessee at Chattanooga. Get access to this full report by clicking here.
Comments