The Transformation of Manufacturing: Workforce Dynamics
- Peak Performance
- Jan 18, 2022
- 5 min read
Updated: Jan 25, 2022
This article is based on the findings in the report, Understanding the Impacts of Industry 4.0 on Manufacturing Organizations and Workers, prepared for the Smart Factory Institute and written by Chris Cunningham, PhD, UC Foundation Professor of Psychology, and Scott Meyers, Graduate Assistant, Psychology Department & Smart Factory Institute, from the Industrial and Organizational Psychology Department at the University of Tennessee at Chattanooga.
As a segment of the American workforce, manufacturing is substantial. Out of a total American workforce of around 160 million, an estimated 13.89 million people were employed in the private sector manufacturing industry in 2020 (Bureau of Labor Statistics [BLS], 2021a; 2021d; 2021e; Worldbank, 2021a). Broadening to consider North America overall by including the total Canadian workforce of around 20 million and the Canadian manufacturing workforce of around 1.66 million, the combined manufacturing workforce of these two countries constitute around 8.6% of the total North American workforce (Statcan, 2021; Worldbank, 2021a; 2021b). This estimate is corroborated by similar statistics reported by the National Association of Manufacturers (NAM, 2020a), that 8.51% of the American workforce in 2018 was in manufacturing. More specifically, within the state of Tennessee, manufacturing employed 11.47% of the workforce in 2020 (NAM, 2020b).

In 2020 and 2021, although all industries and individuals were impacted by the COVID-19 pandemic, data indicate that the manufacturing industry was fairly stable and showed signs of earlier recovery than many other industries, at least in some ways. As in other industries, manufacturing took a major employment hit: In August 2021, manufacturing employment in the US was down by 378,000 jobs from pre-pandemic numbers in February 2020 (BLS, 2021c). However, manufacturing employment numbers have been on the rise since that report, with the industry steadily increasing sector employment since May 2021 with 36,000 jobs followed by similar and consistent growth to 37,000 jobs in August 2021 (BLS, 2021c). The Manufacturing Purchasing Managers Index (PMI®) from the Institute of Supply Management's September report (Institute of Supply Management [ISM]; 2021) registered 61.1%, indicating strong manufacturing sector expansion and U.S. economic growth in September 2021. In 2020, U.S. manufacturing contributed a significant USD 2.27 trillion to the U.S. Gross Domestic Product (GDP) (Bureau of Economic Analysis [BEA], 2020). Within Tennessee, manufacturing accounted for 15.32% of total output in the state (NAM, 2020b).
A variety of labor management challenges have been reported within manufacturing during the COVID-19 pandemic period (ISM, 2021). Difficulties in hiring and a clear cycle of labor turnover are particular challenges for this industry at the time of this report (ISM, 2021). The turnover issue especially is a sustained problem for manufacturing in general, and an increasing challenge for manufacturers in the southern United States over recent years (Table 1).

Source: “Economic News Release,” BLS (2021b)
Note: Annual total separation rates are the total amount of separations per year as a percent of the annual average employment.
Extending from the data summarized in Table 1, 47% of ISM respondents in the September 2021 PMI® report expressed difficulties filling positions and retaining workers; these issues were noted to have increased in survey comments beginning in August 2021 from prior months (ISM, 2021). Furthermore, there is an overall trend of rapidly decreasing numbers of employees in private sector manufacturing jobs from 1985 to the present (BLS, 2021d). Consistent with this larger trend of declining employment, when examining manufacturing specifically in the Southeast, manufacturing employment and number of firms have steadily decreased over the past 30 years; much of this employment loss was attributed to firm closures in the southeast from 1990 to 2019 (Zhang, 2021). To provide a more specific example, Tennessee experienced a 6.21% decrease in the number of manufacturing firms during this time. Furthermore, by examining total manufacturing employee headcount over this period, it can be estimated that Tennessee experienced a 28.8% decrease in overall manufacturing employment from 1990 to 2019 (BLS & Federal Reserve Bank of St. Louis, 2021). This would indicate a 30-year trend of Tennessee experiencing both declining employment and numbers of firms in manufacturing. This is especially critical as Tennessee makes up 8.2% of Southeast regions total manufacturing employment (Zhang, 2021). Whether examining current trends or historical data, manufacturing has experienced, is experiencing, and will likely continue to experience a variety of serious labor management concerns. It is also important to note, however, that the overall separation rates within manufacturing are consistently below the overall rates and rates for many other core industry areas such as mining and construction (BLS; 2021b). An implication of this, is that although manufacturing faces critical issues with labor management that require critical consideration, it is a more stable sector of employment compared to other industries.
Figure 1. Manufacturing Industry Productivity and Headcount Over Time

Despite these general employment trends, manufacturing industry output is expected to drastically increase in the near future to meet increasing global demands. Although DataUSA (2021) reports estimate a -3.46% change in overall manufacturing industry jobs over the next 10 years (due to high rates of separation and lower than necessary numbers of interested, available, and skilled talent to fill positions), the projected output growth for this industry is 16.4%. The challenge here more clearly, the manufacturing industry will need to produce more with fewer workers. This is only going to be possible with more widespread adoption of Industry 4.0 technologies and practices that improve how efficiently manufacturing work is done, with a blended approach of human, machine, and human-machine augmented work arrangements supported by advanced technologies. This combination of a decreasing workforce and increasing overall demands also highlights the critical need for widespread workforce development efforts to prepare the existing and emerging workforce for Industry 4.0 technologies and processes.
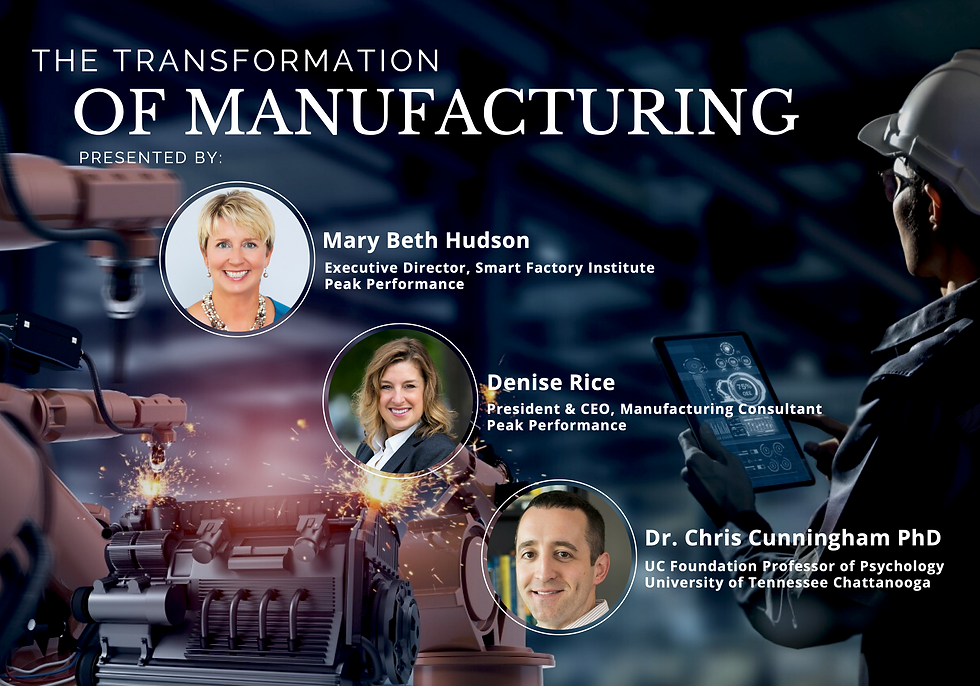
Join us LIVE as we explore the current manufacturing industry and the challenges and opportunities it faces in the midst of the adoption of Industry 4.0. The Transformation of Manufacturing will be a 3-stop tour across the state of Tennessee with stops in Jackson, Chattanooga, and Smyrna beginning February 2, 2022.
Each session builds on the prior session. In-person and virtual attendance options are available. Join us in person at your local session and virtually for the other two sessions!
February 2, 2022 | 7:30am - 8:30am (CT)/8:30 - 9:30am (ET)
Location: Jackson Chamber of Commerce, 197 Auditorium Street, Jackson, TN 38301 In-Person & Virtual Attendance Options Available
February 9, 2022 | 7:30am - 8:30am (CT)/8:30 - 9:30am (ET)
Location: LIVE from the Smart Factory Institute, Chattanooga, TN
Virtual Attendance Only
February 16, 2022 | 7:30am - 8:30am (CT)/8:30 - 9:30am (ET)
Location: TCAT Smyrna/Nissan Training Center, 663 Ken Pilkerton Dr., Smyrna, TN 37167 In-Person & Virtual Attendance Options Available
Sessions are free to attend, registration is required.
This tour is based on the findings in the report, Understanding the Impacts of Industry 4.0 on Manufacturing Organizations and Workers, prepared for the Smart Factory Institute and written by Chris Cunningham, PhD and Scott Meyers from the Industrial and Organizational Psychology Department at the University of Tennessee at Chattanooga. Get access to this full report by clicking here.
Commentaires